Production Process Flow and Inspection Flow
With over 9000 highly skilled employees and 293 advanced production lines spread across 13 factories, we have produced 20 million tons steel pipes in 2022, and the sales amount has beyond 160 million US Dollars in 2018. For 17 consecutive years, Youfa is titled among TOP 500 Enterprises in China Manufacturing Industry since 2006.
Hot-Dipped Galvanized Steel Pipe
Manufacture Procedures
01.Unpacking/Inspection→02.Picking&Solvent→03.Drying→04.SHot dipped galvanizing→05.Outside blasting/Inside cooling→06.Water cooling→07.Passivation→08.Proceed inspection→09.Marking→10.Packing→11.Final examination&Storage
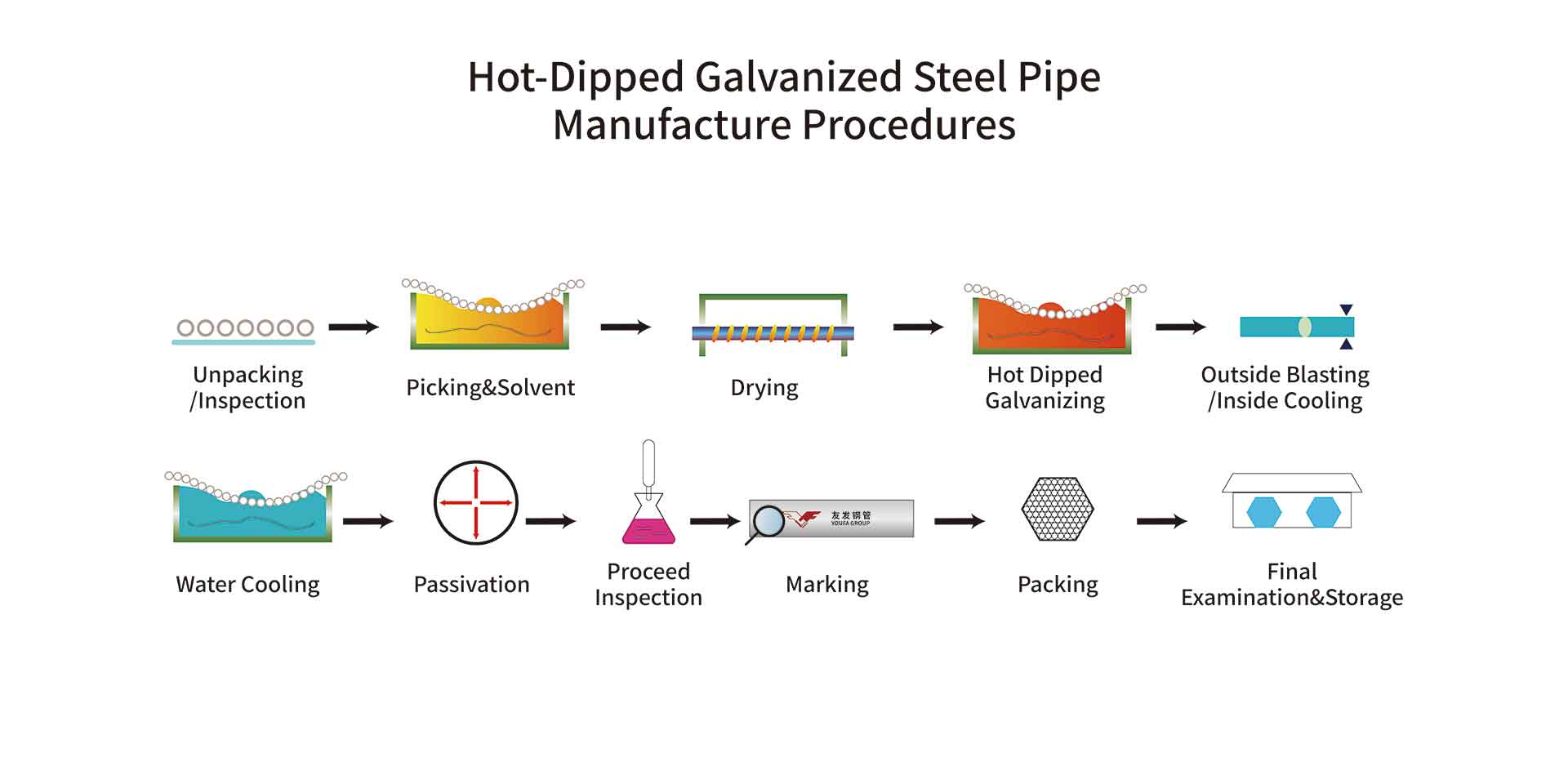
Hot-Dipped Galvanized Steel Pipe
Inspection Flow chart
01.Charging/Unpacking→02.Pickling→03.Washing→04.Solvent/Drying→05.Hot dipped galvanizing→06.Air cooling/Water Cooling→07.Passivation/Drying→08.Marking→09.Product examination→10.Zinc layer thickness inspection→11.Physical and chemical test→12.Final examination
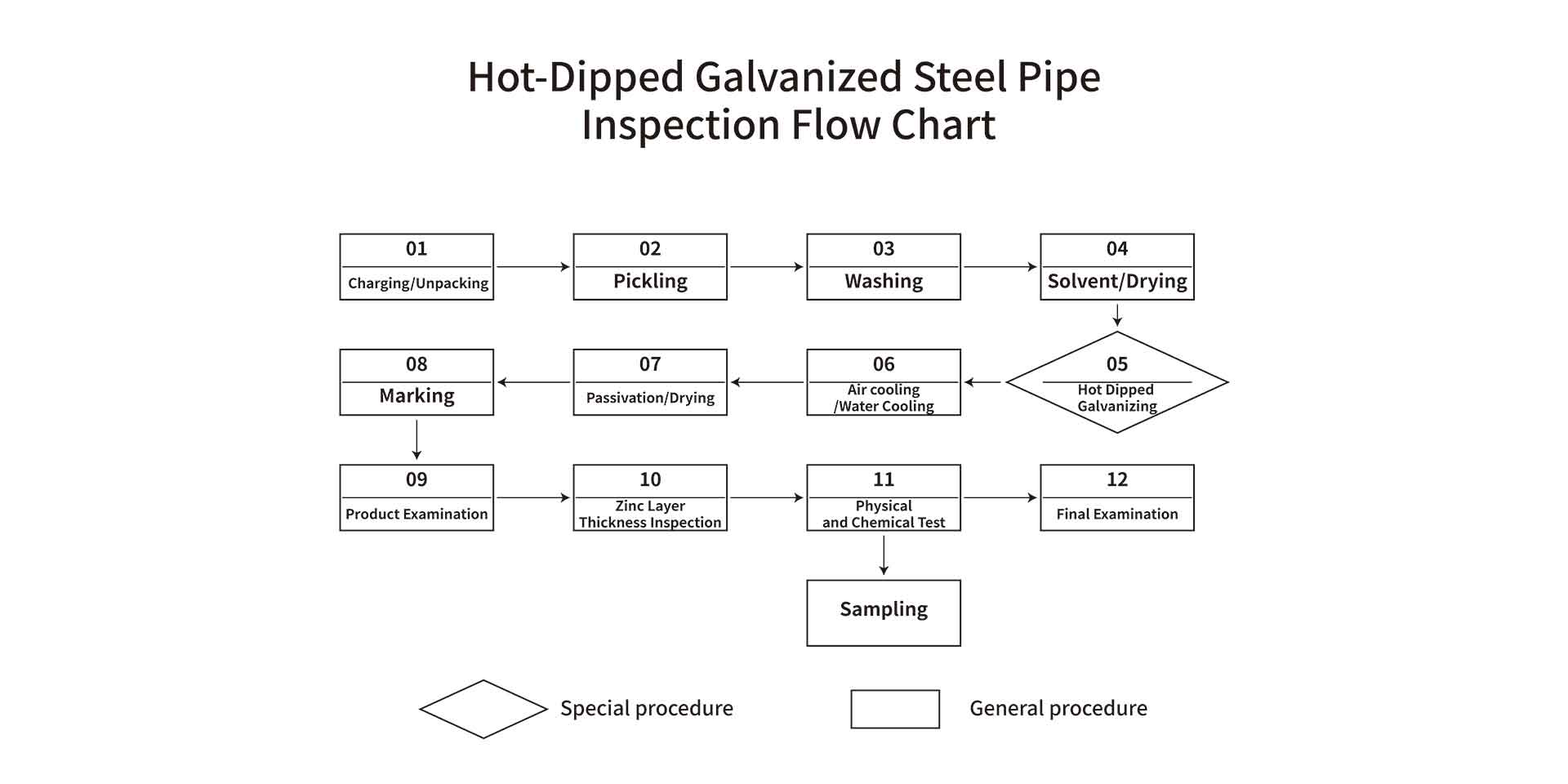
Electrical Resistance Weld Pipe-ERW
Manufacture Procedures
01.Open volume→02.Correction/The first cut/Welded→03.Loop storage→04.Figuration system→05.Welding/Remove inside and outside burr→06.Welding seam heat treatment→07.Air-cooled/Water-cooled/Estaiblishen in diameter/Correction→08.Flying saw cut→09.Exterior inspection/Marking→10.Plain end and bevel end→11.Hydraulic test→12.Ultrasonic inspection→13.Pipe end Ultrasonic inspection→14.Weighting/Record→15.Put in storage
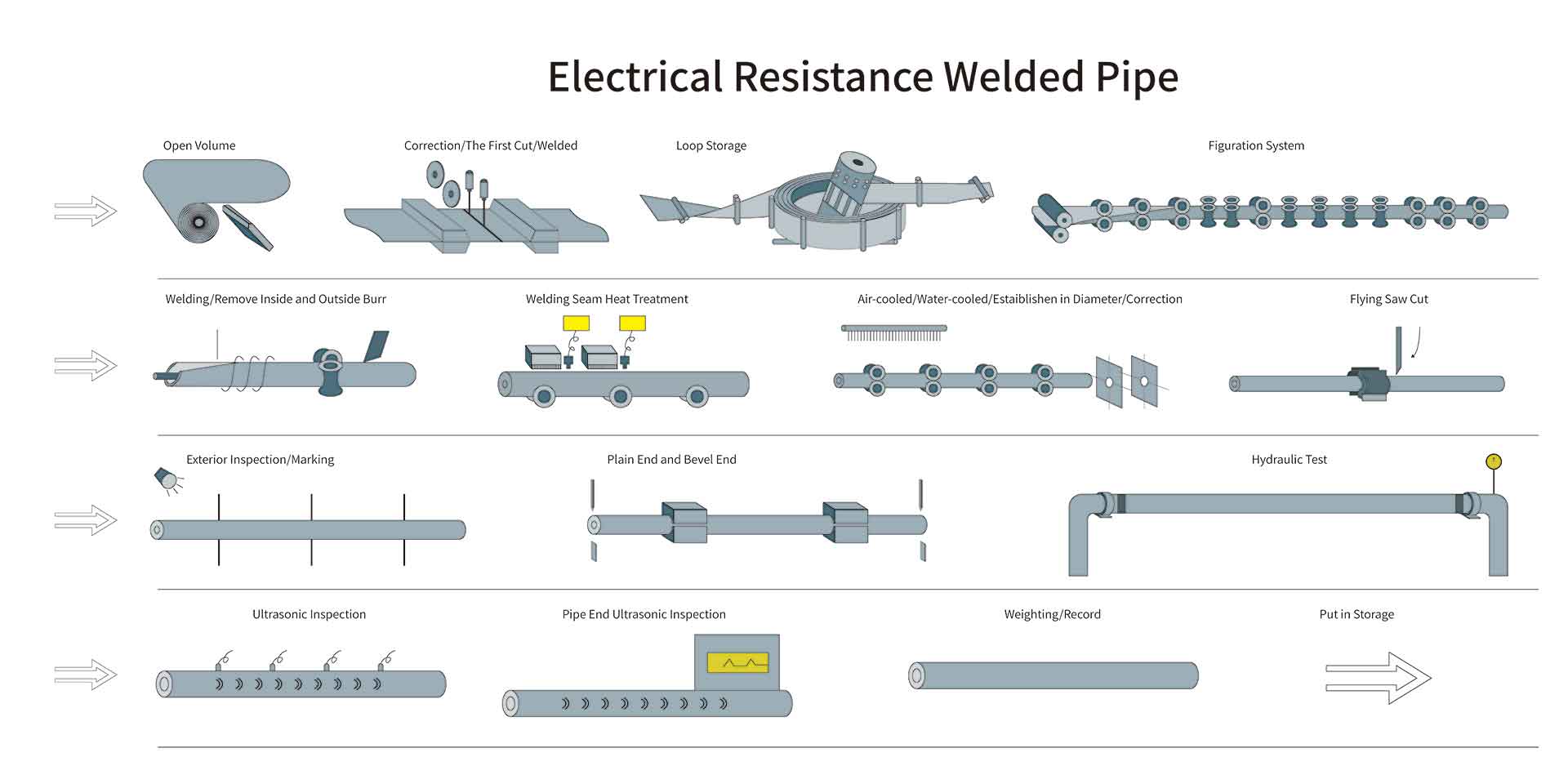
Electrical Resistance Weld Pipe-ERW
Inspection Flow chart
01. Raw material inspection →02.Cutting inspection →03.Charging inspection →04.Welding inspection→05.Visual inspection→06.Repair pipe inspection →07.Finished examination
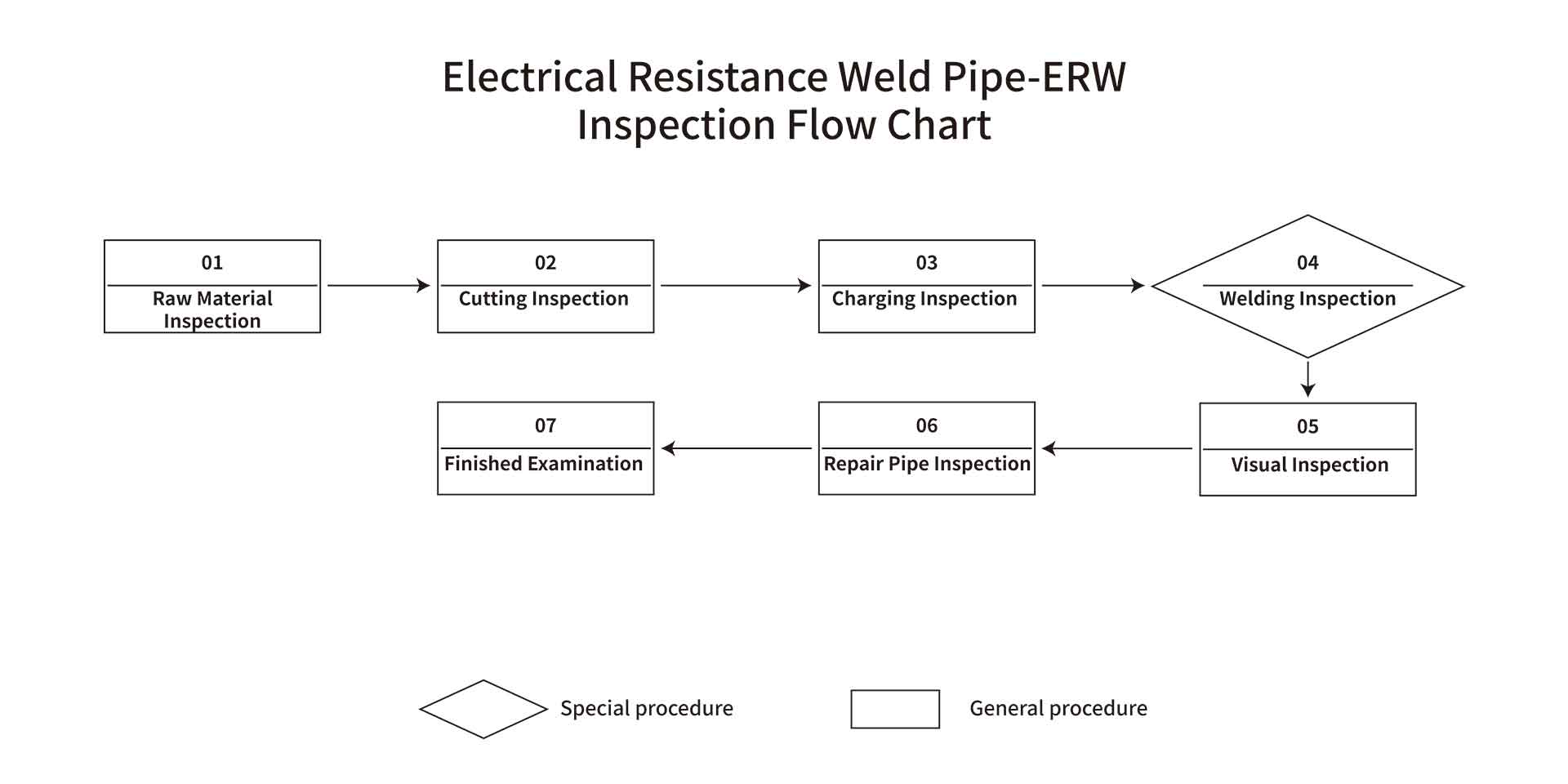
We will test raw materials and production processes according to different standards to ensure that the products meet the standards or contract requirements.
Square/Rectangular Welding Steel Pipe
Inspection Flow chart
01. Raw material inspection →02.Cutting inspection →03.Charging inspection →04.Welding inspection→05.Visual inspection→06.Repair pipe inspection →07.Finished examination
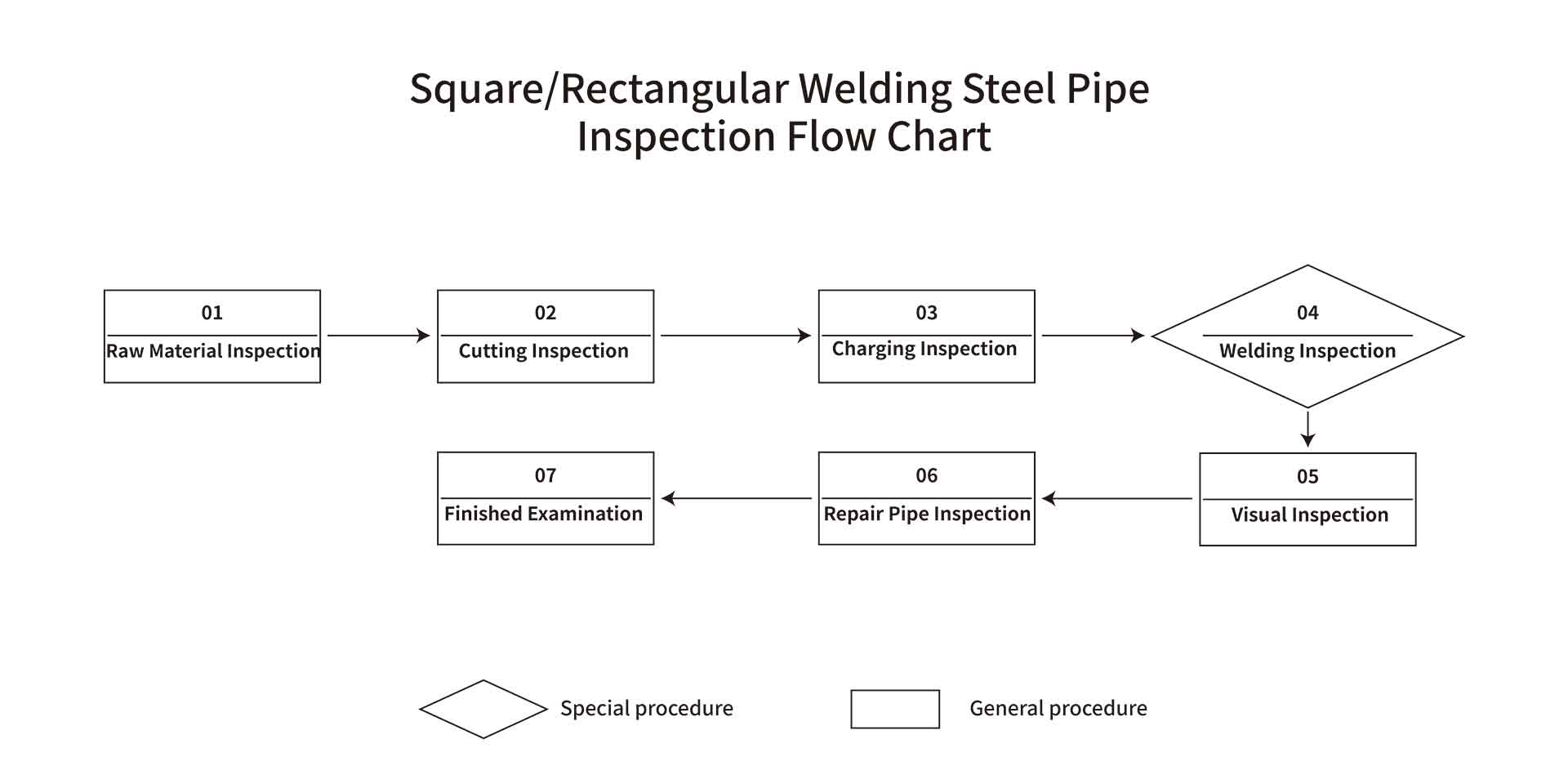
Square/Rectangular Welding Steel Pipe
Manufacture Procedures
01. Steel strip inspection→02.Split→03.Uncoiling/Charging→04.Shear&Weld→05.Coil Flatten/Loop storage→06.Cold roll forming→07.High Frequency welding→08.Weld scraping scar→09.Water cooling→10.Sizing→11.Cut off→12.Process inspection→13.Marking/Packing→14.Inspection→15.Weighting/Put in storage→16.Final examination
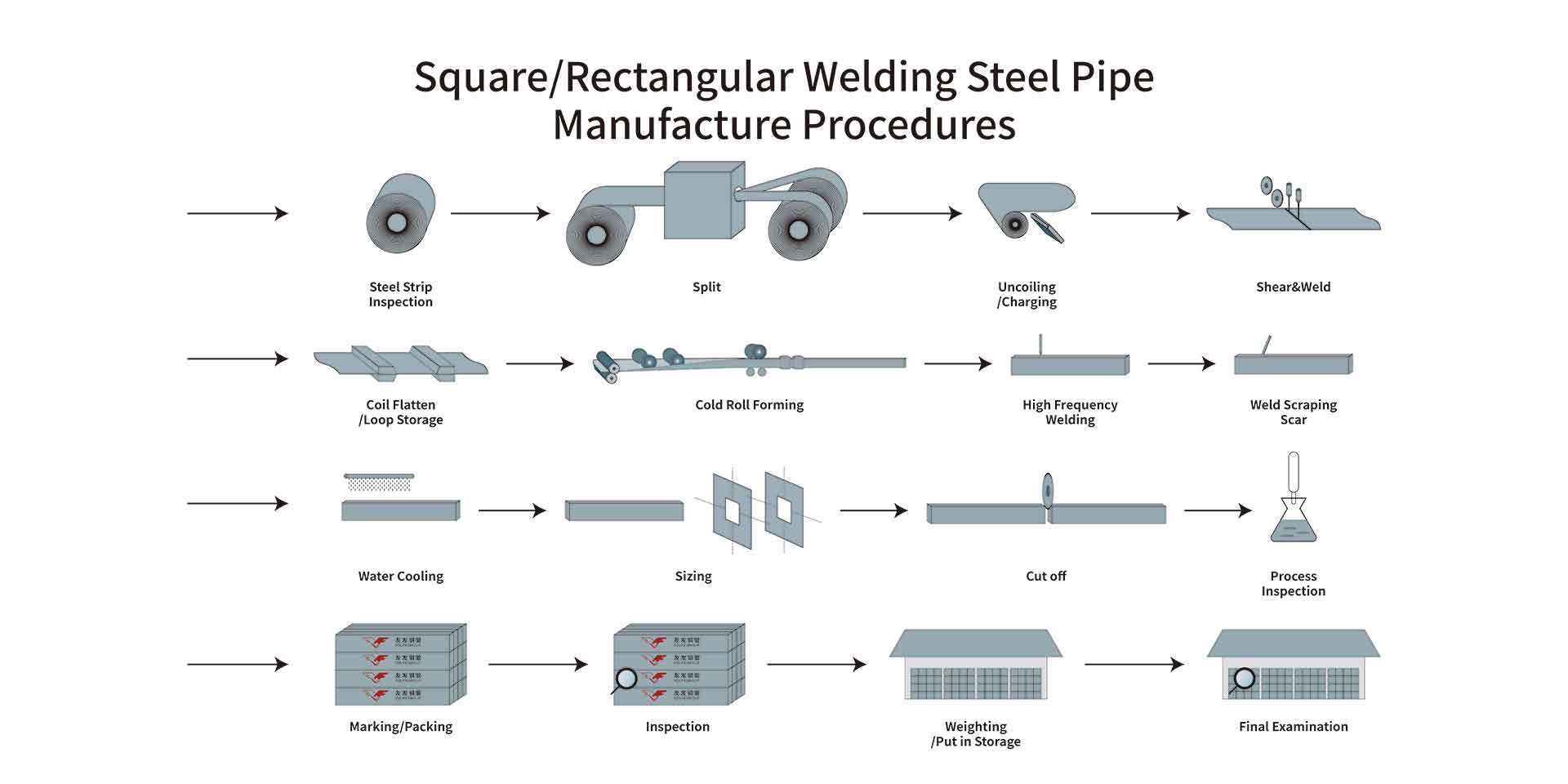
Hot-Dipped Square/Rectangular Welding Steel Pipe
Inspection Flow chart
01. Raq material inspection→02.Pickling inspection→03.Hot Dipped Galvanizing inspection→04.Sprinkling Passivation inspectiion→05.Marking inspection→06.Packing inspection→07.Final examination
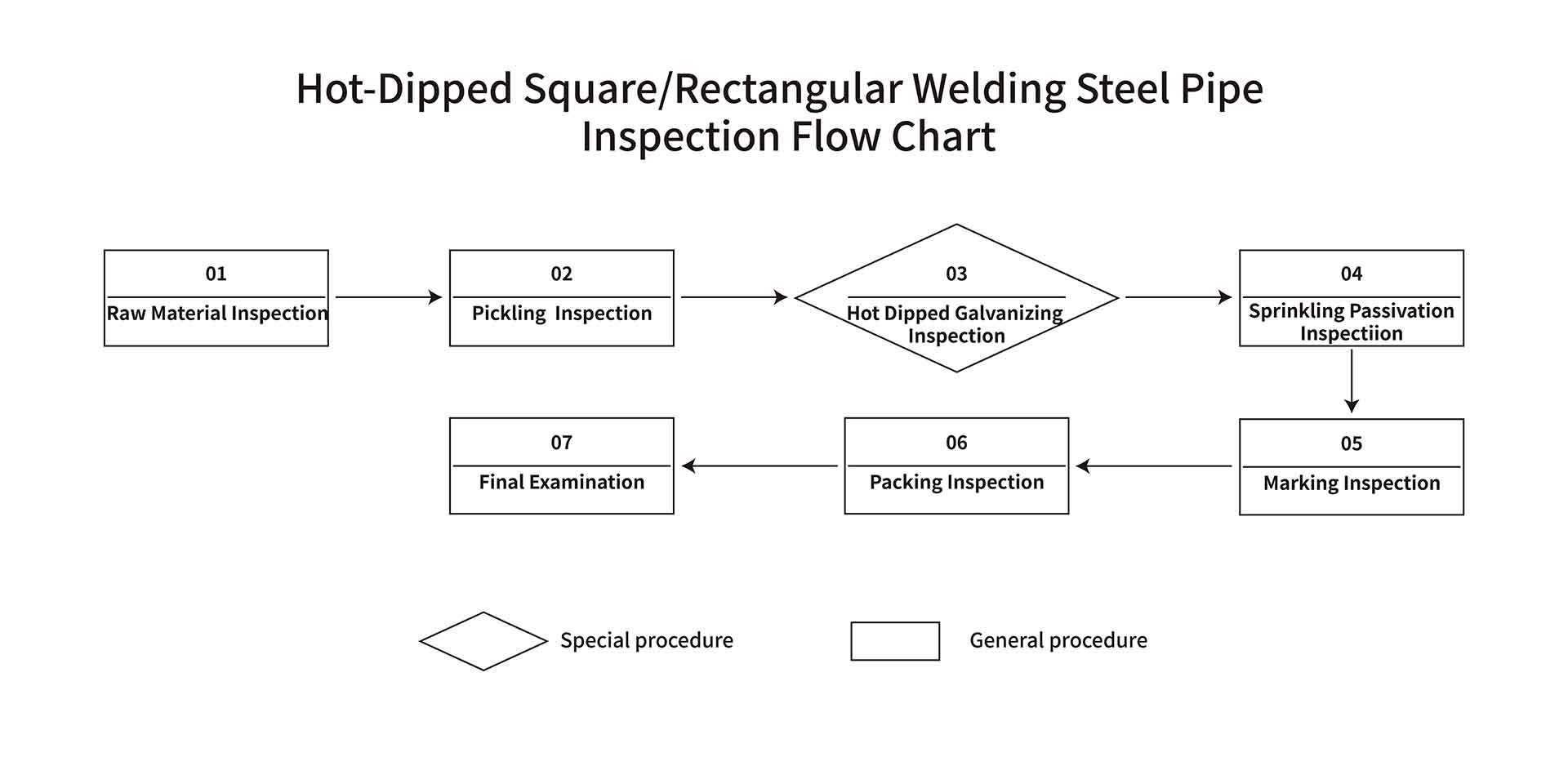
We will test raw materials and production processes according to different standards to ensure that the products meet the standards or contract requirements.
Hot-Dipped Square/Rectangular Welding Steel Pipe
Manufacture Procedures
01.Welding steel pipe→02.Unpacking/Charging→03.Pickling→04.Washing→05.Solvent→06.Drying→07.Hot Dipped Galvanizing→08.Outside Blasting→09.Inside Cooling→10.Air-cooled/Water-cooled→11.Semi-finished products inspection→12.Passivation→13.Marking→14.Packing→15.Inspection→16.Weighting/Storage→17.Final Examination
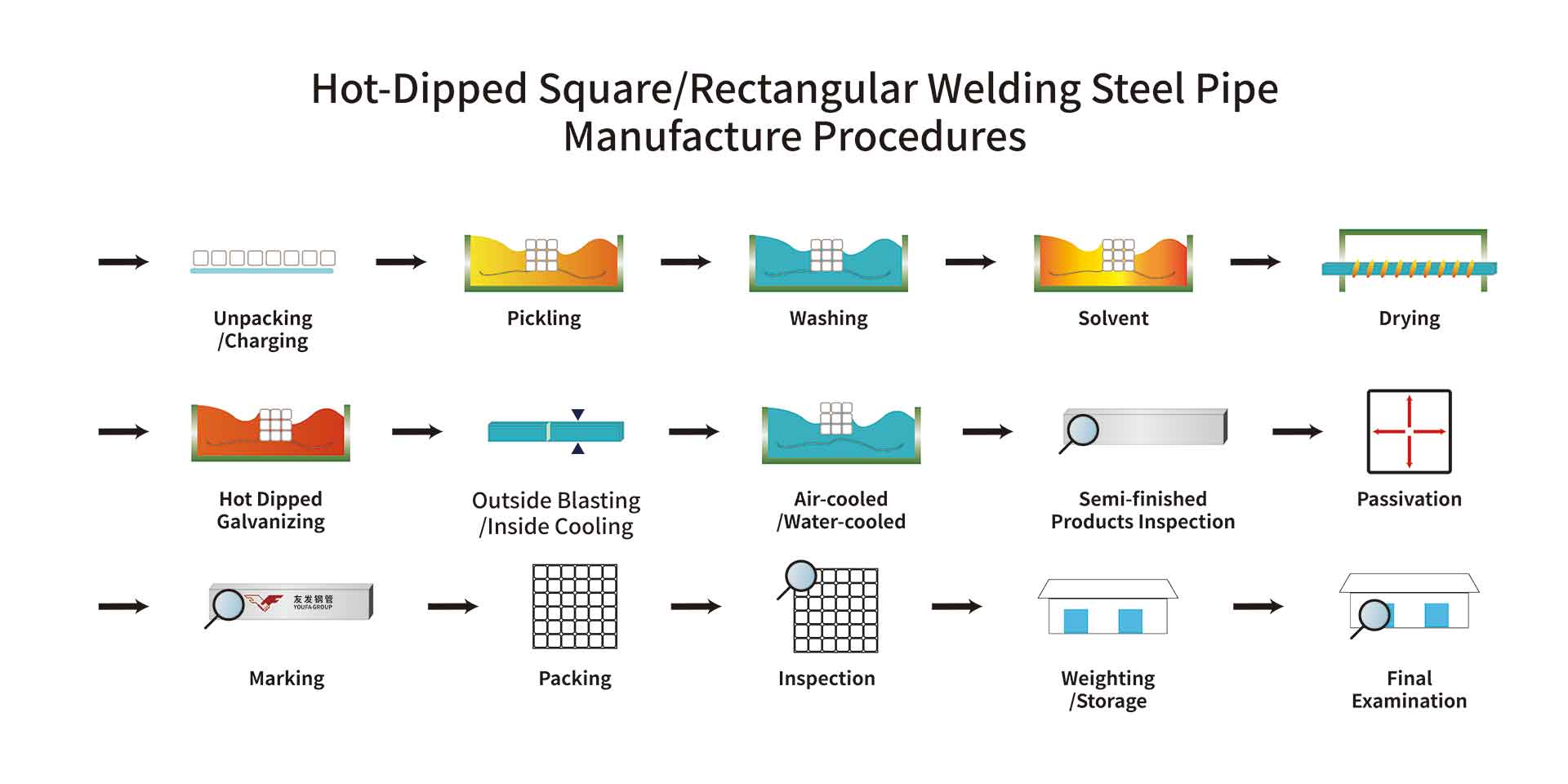
ERW oil and gas pipeline
Inspection Flow chart
01. Raw material inspection→02.Welding(Metallographic examination)→03.Outer diameter length inspection→04.Flat test→05.Sampling→06.Physical and chemical test→07.Hydraulic test→08.NDT(nondestructive testing)→09.Final Examination
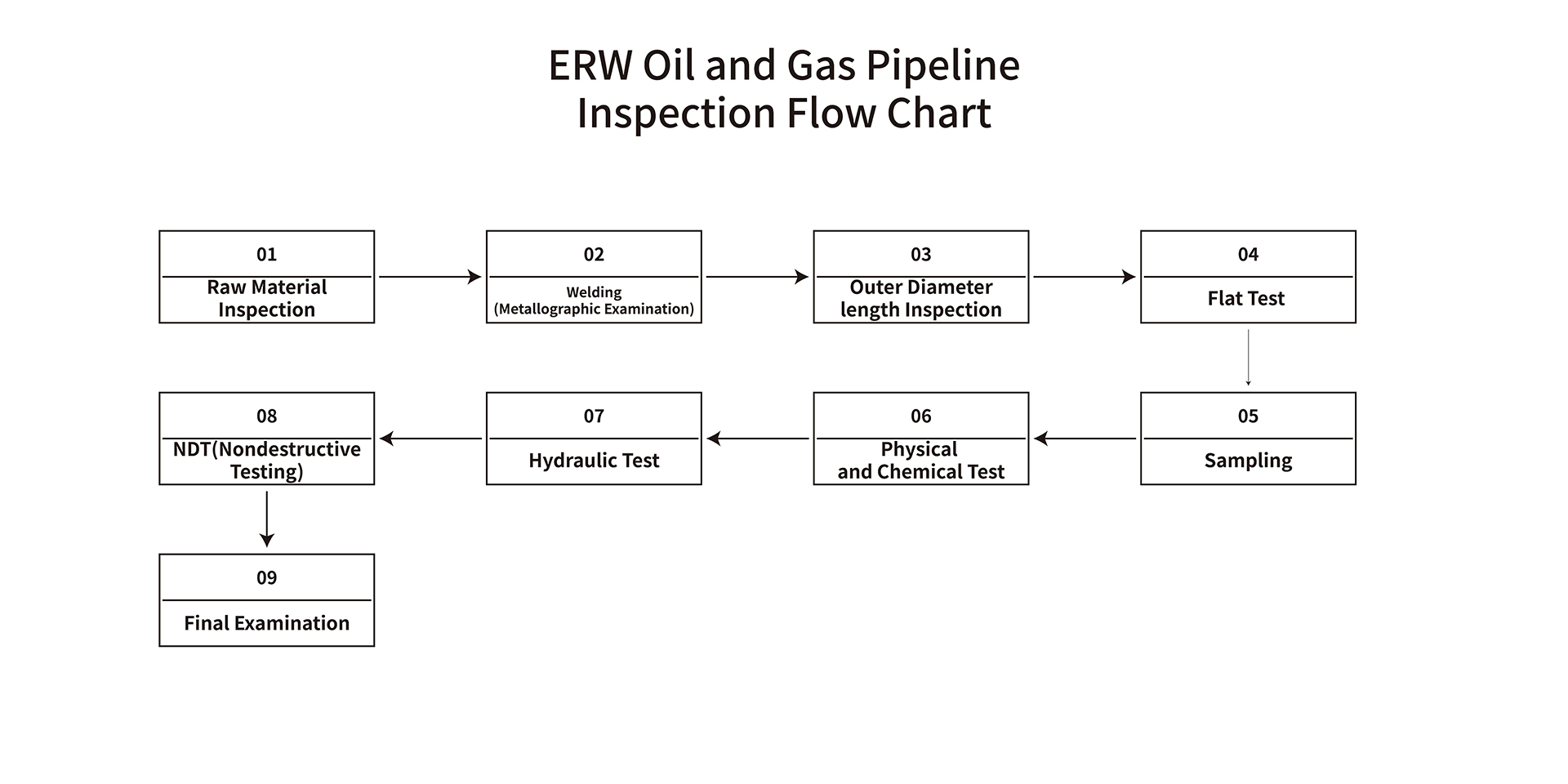
We will test raw materials and production processes according to different standards to ensure that the products meet the standards or contract requirements.
01.Open volume→02.Correction/The first cut/Welded→03.Loop storage→04.Figuration system→05.Welding/Remove inside and outside burr→06.Welding seam heat treatment→07.Air-cooled/Water-cooled/Estaiblishen in diameter/Correction→08.Flying saw cut→09.Exterior inspection/Marking→10.APlain end and bevel end→11.Hydraulic test→12.Ultrasonic inspection→13.Pipe end Ultrasonic inspection→14.Weighting/Record→15.Put in storage
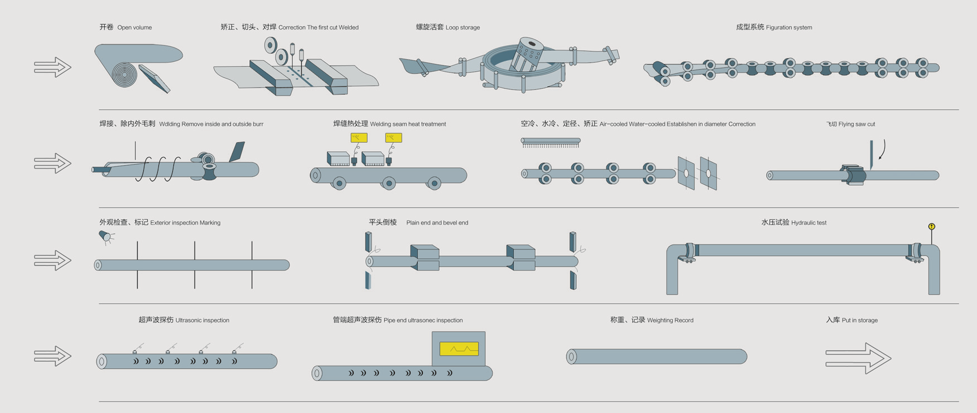
Electrical Resistance Weld Pipe-ERW
Manufacture Procedures
01. Raw material inspection→02.Marking&Put in storage→03.clipping→04.Put in storage/Inspection→05.Sheer&Weld→06.Physical and chemical test→07.Cut off→08.Sizing→09.Inspection→10.Packing→11.Weighting→12.Scan codes
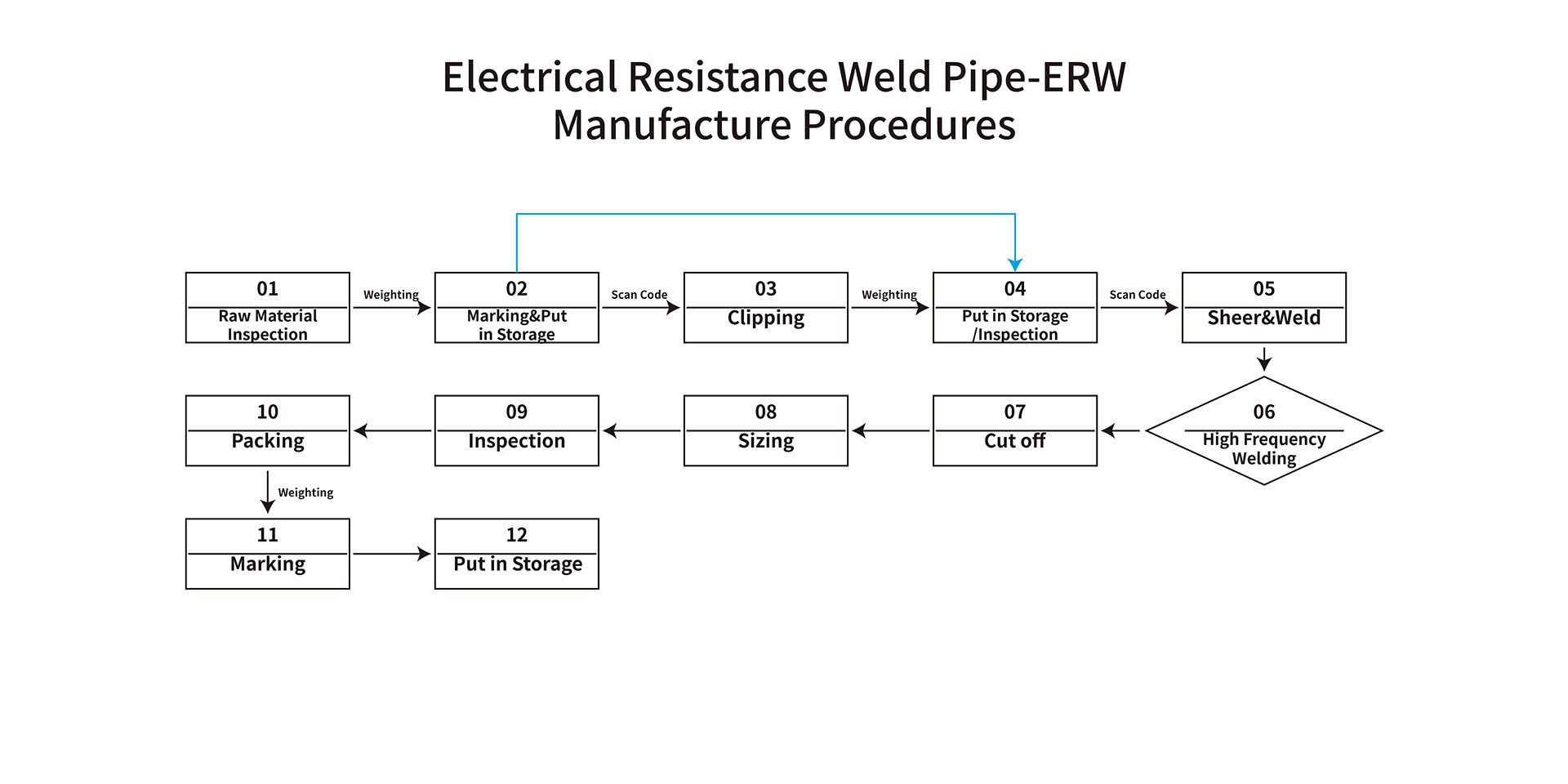
Ringlock Scaffolding System(Ringlock Standard)
Manufacture Procedures
01.Raw material inspection→02.Saw cutting (punching)/Rosette feed/Spigot feed→03.Welding→04.Packing/inspection→05.Marking/Put in storage
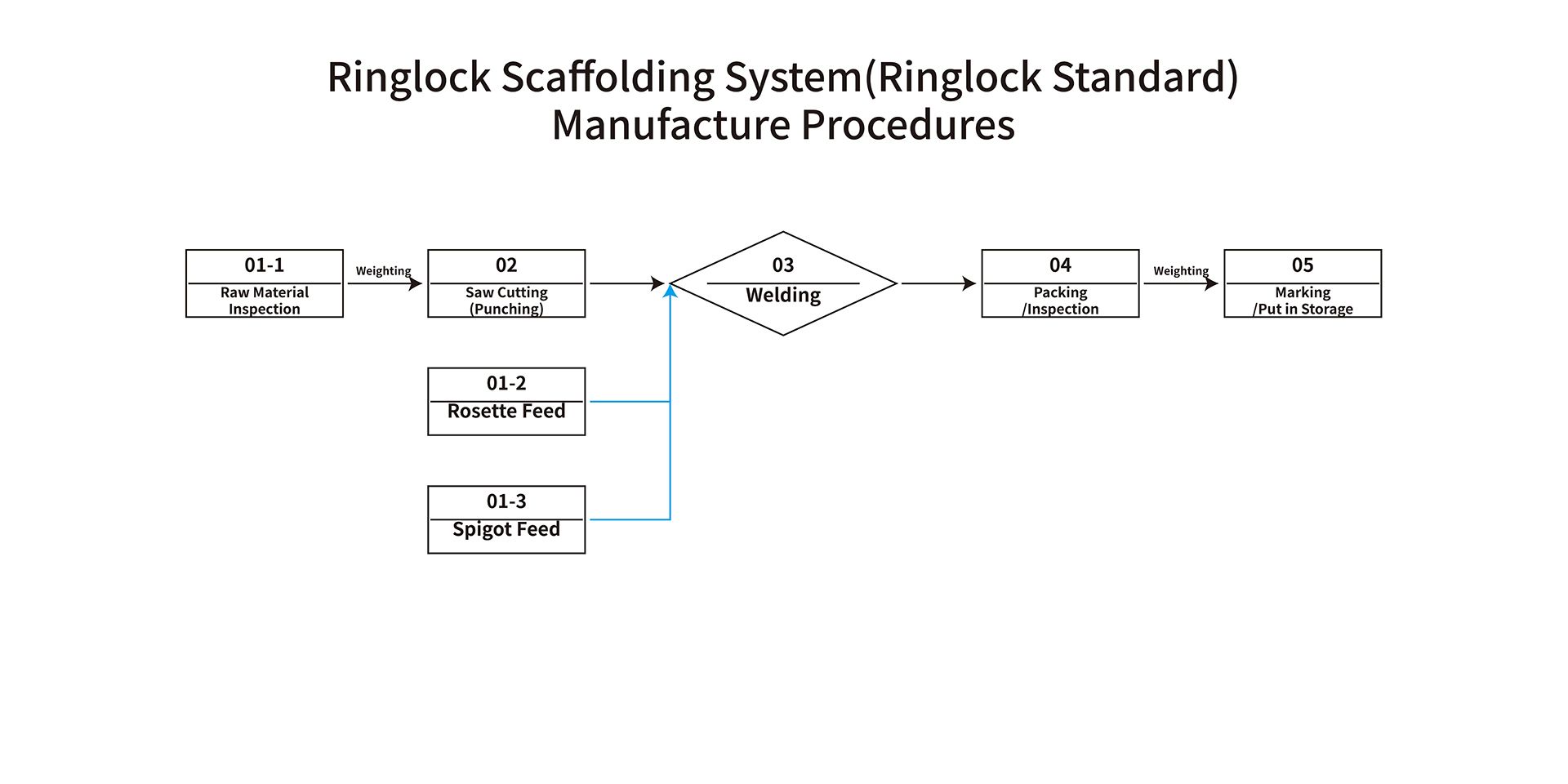
Ringlock Scaffolding System(Ringlock ledger)
Manufacture Procedures
01.Raw material inspection→02.Cut off/Ledger end Feed→03.Welding→04.Packing/inspection→05.Marking/Put in storage
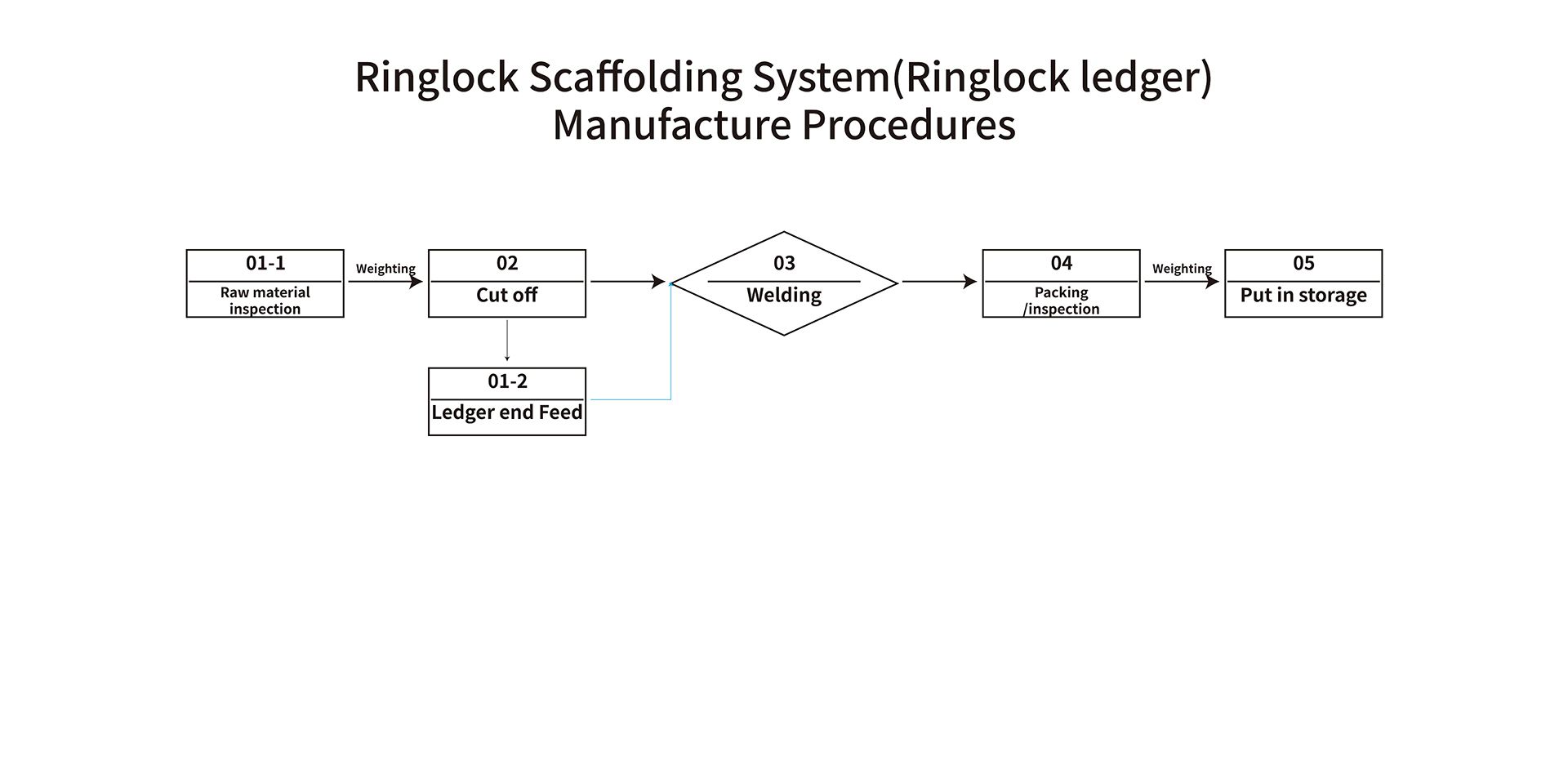
Ringlock Scaffolding System(Stamping)
Manufacture Procedures
01.Raw material inspection→02.Stamping→03.Packing/Inspection→04.Put in storage
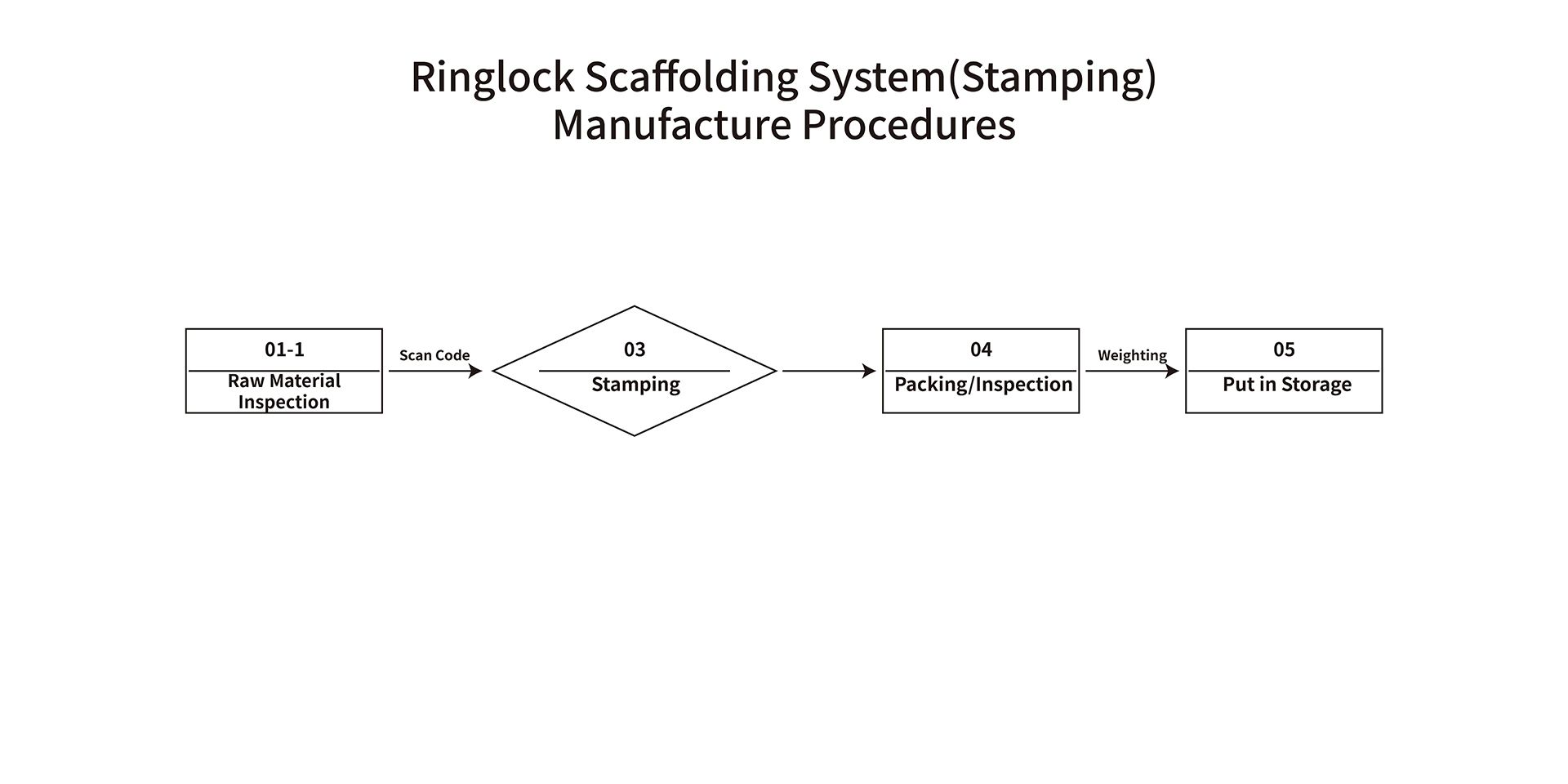
Ringlock Scaffolding System(U head jack、Jack base)
Manufacture Procedures
01.Raw material inspection→02.Cut off→03.Screw rolling/Inspection/Uhead jack /jack base feed→04.Welding→05.Packing/inspection→06.Put in storage
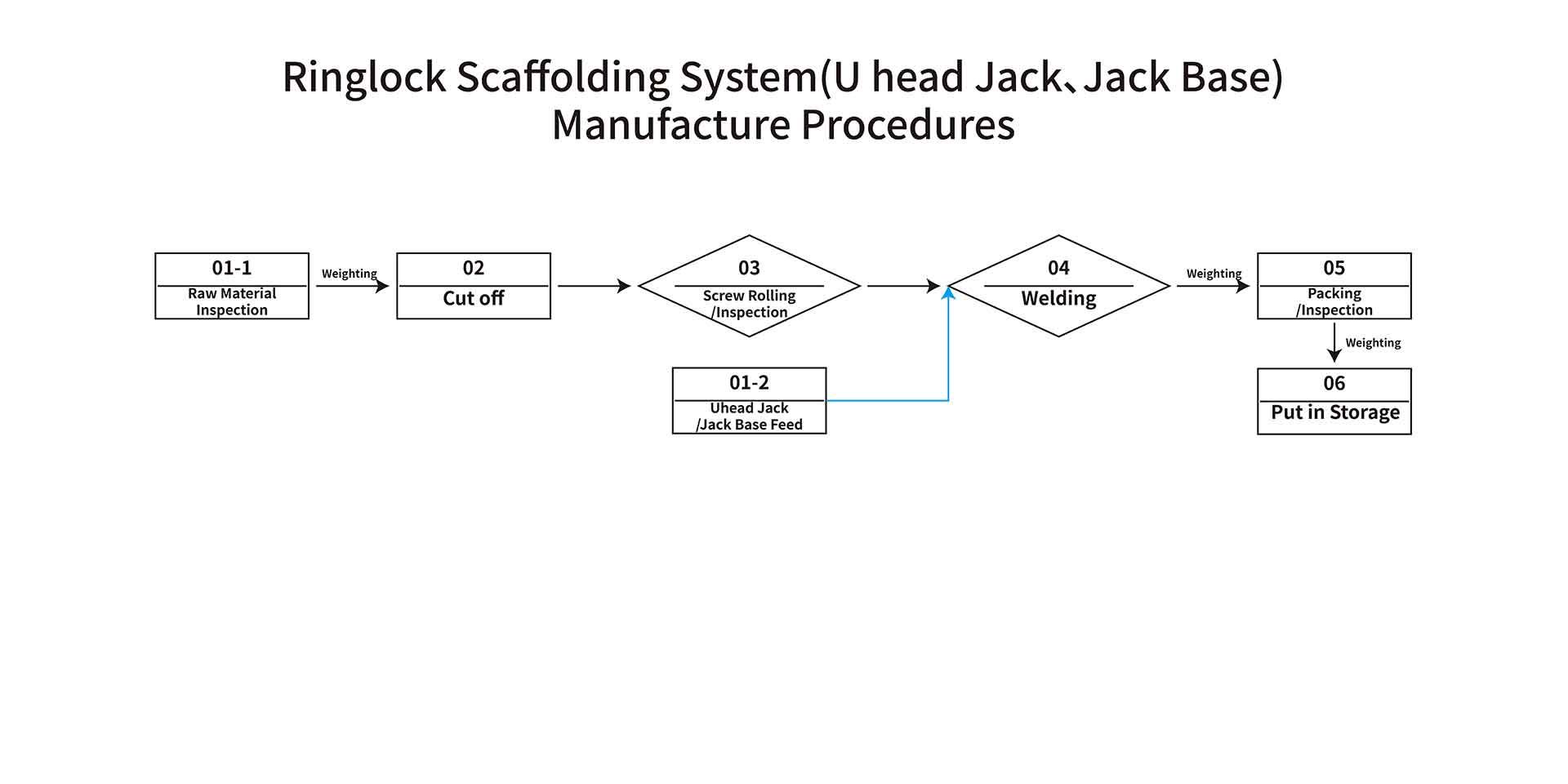
Ringlock Scaffolding System(Ringlock diagonal brace)
Manufacture Procedures
01.Raw material inspection/Wedger pin/Pin/Brace head→02.Baiting inspection/edger pin/Brace head baiting→03.Welding→04.Packing/inspection→05.Put in storage
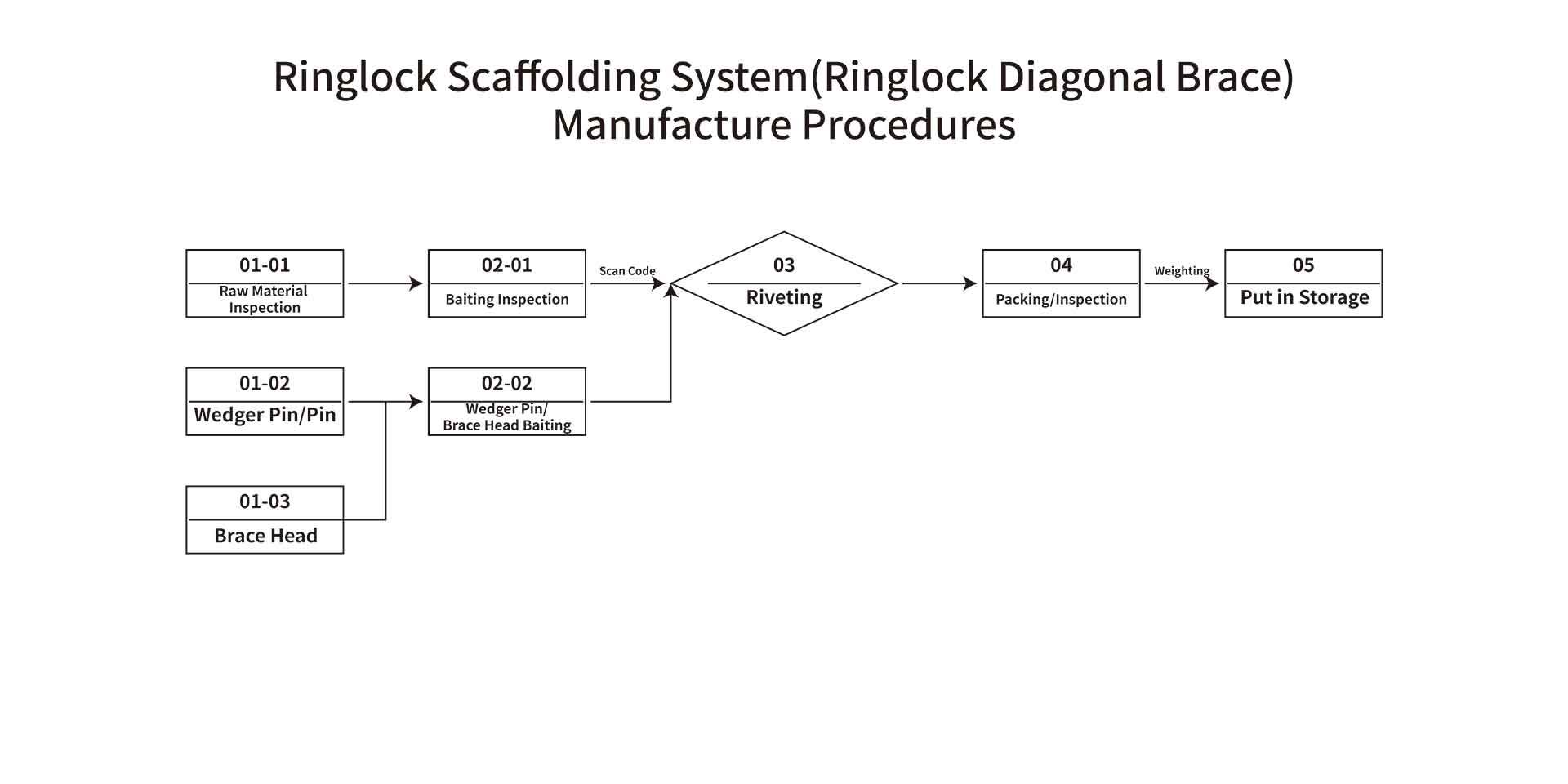