Beveling carbon steel pipes is a critical preparatory step for welding, ensuring strong, reliable joints.
Beveled Carbon Pipes Advantages
1. Weld Penetration and Joint Strength:
Deeper Weld Penetration: A beveled edge creates a groove that allows the weld metal to penetrate deeply into the joint, forming a stronger bond than a square-edged weld.
Stress Distribution: The angled geometry distributes mechanical stresses more evenly, reducing the risk of cracks or failures under pressure.
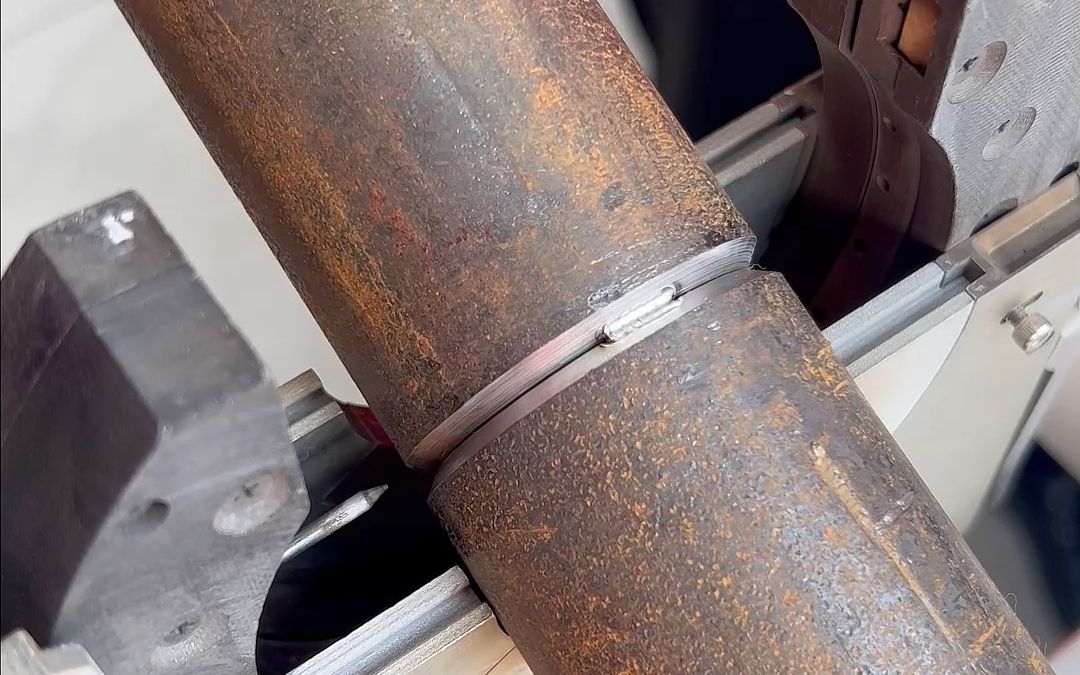
2. Material Thickness:
Thick-Walled Pipes: Beveling is essential for thicker pipes to ensure sufficient weld material deposition, preventing weak joints in high-pressure systems.
3. Edge Preparation:
Smooth Surfaces: Removes burrs or irregularities from cutting, providing a clean surface for welding.
Root Face and Gap Control: Ensures proper root face dimensions and gap spacing, critical for weld quality.
4. Alignment and Fit-Up:
Easier Assembly: Beveled edges aid in aligning pipes during fit-up, minimizing misalignment and ensuring uniform weld profiles.
Pipe Ends Beveled Quality Control
Standardized groove parameters (such as V-shaped grooves of 30 °) facilitate the inspection of welding quality and ensure that the joint meets strength and airtightness requirements.
Exceptional Circumstances
Thin walled pipelines (such as wall thickness ≤ 3mm): flat butt welding without bevel can be used, or only slight chamfering is required.
Non pressure pipelines: Low pressure, non critical use pipelines may simplify groove requirements, but the industrial field generally requires strict groove processes.
Post time: Mar-17-2025